New Calibration Method Improves Semiconductor Digital Twins
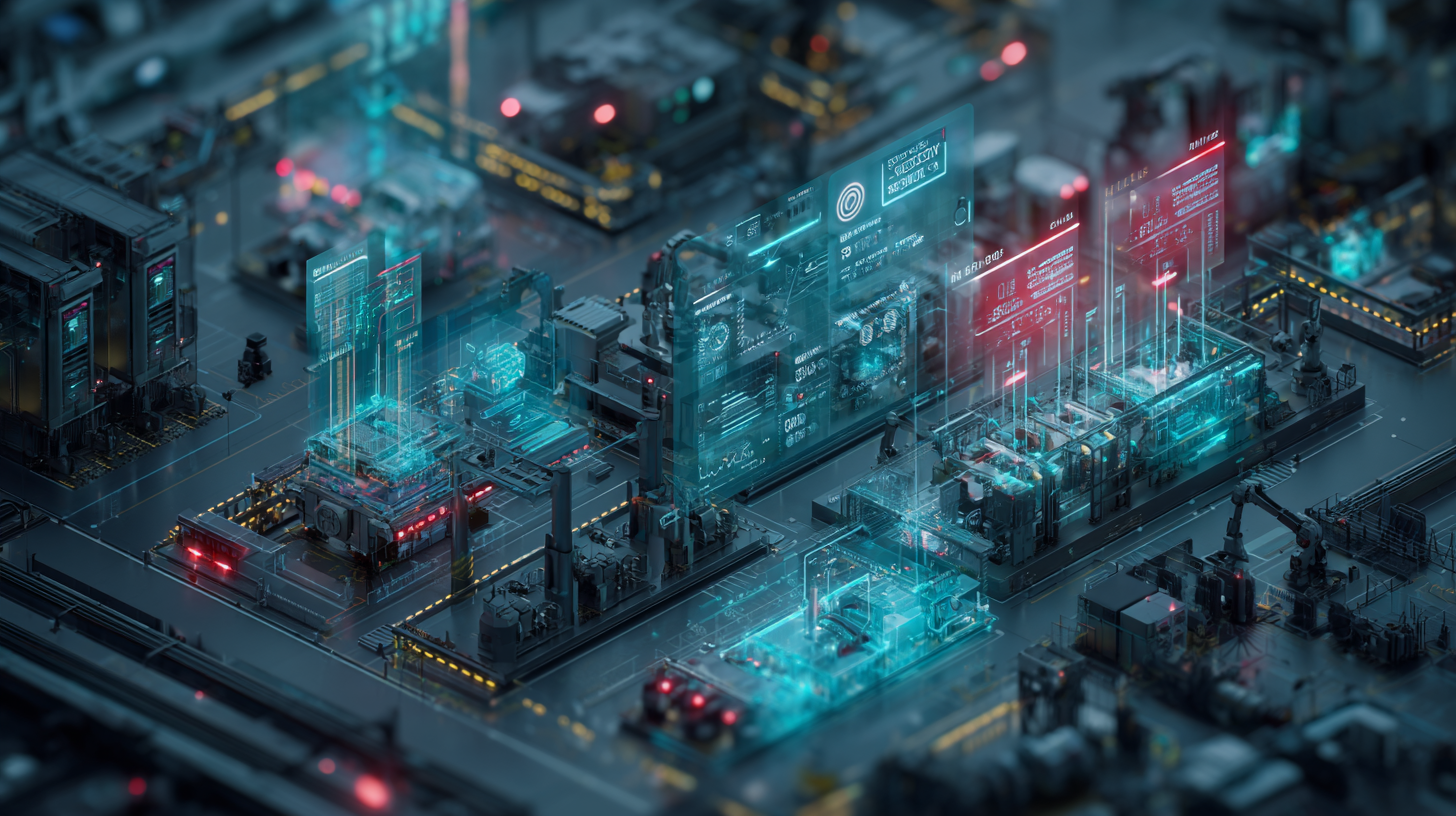
- A new Bayesian method from Pusan National University improves the accuracy of digital twins used in automated material handling systems for semiconductor fabrication, using less real-world data.
- Tested across multiple scenarios and already in use at Samsung Display, the approach handles both uncertain values and system differences.
Digital twins of real factory systems are widely used to manage production. In semiconductor fabrication, these virtual models of automated material handling systems (AMHSs) help track complex flows of machines, transporters, and storage. But these models often miss fine-grained details like slight changes in machine speed or simplify control logic, which reduces their accuracy. To solve this, a team led by Professor Soondo Hong at Pusan National University developed a smarter calibration method.
The team used a Bayesian approach that combines field data with simulation results to correct for uncertain parameters and discrepancies. It relies on Gaussian processes to adjust predictions across different scenarios. In tests, their model outperformed a basic calibrated twin and a field-only prediction model.
Published in the Journal of Manufacturing Systems on June 1, 2025, the framework is reusable, customizable to each facility, and scalable to large systems. It's now being applied at Samsung Display, where it supports fast calibration and better decision-making in complex environments.
🌀 Tom’s Take:
Digital twins usually break down when there’s not enough data or when real systems behave differently than expected. This method handles both. It brings digital models closer to the messy details of how things really work, and does it without needing mountains of data.
Source: EurekAlert!